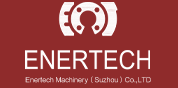
Classification:common problem Release time:2021-05-11 35 Article source:common problem Release time:2021-05-11 35
When using the electric stop valve, there will be some faults, which will affect our normal use, so it needs to be solved in time. What are the common faults?
1、 The electric stop valve operates normally, but cannot withstand regulation
Cause: the valve core is closed or the pipe is blocked.
Solution: close the valve core. The valve core and valve stem are firmly connected, and the pipeline is dredged in time.
2、 Non action of check valve
Cause: there is no signal for pressure or diaphragm crack, diaphragm air leakage, and diaphragm thrust can be reduced; The valve core is stuck with the valve seat or bushing, and the valve rod is bent, which makes the check valve system unable to act.
Solution: connect the signal line and air source connector more firmly. The enterprise may need to replace the diaphragm, straighten the valve stem or directly replace the valve stem.
3、 Unstable or oscillating check valve
Cause: the diameter of check valve is too large, the flow direction of single seat valve medium is consistent with the closing direction, and the valve core and guide sleeve are seriously worn.
Solution: replace the valve with the appropriate valve diameter, adjust the valve direction, improve the bonding surface, or replace the valve core and guide sleeve.
4、 Check valve slow or bouncing
Cause: aging or dry sealing packing increases the friction between valve stem and packing, and the valve body contains viscous dirt, blockage, coking, etc. the diaphragm and "O" sealing ring leak.
Solution: replace the sealing packing, readjust, remove dirt, coking, etc., tighten the membrane head, or replace the diaphragm O-ring.
In case of these system failures during the use and management of pneumatic ball valves, we need to repair them in time.
Contact
Email :admin@enertechmsz.com
Tel:+86 0512-65168207
Add:No. 18, Shiyang Road, Suzhou high tech Zone
Copyright:Enertech Machinery (Suzhou)Co.,LTD
Technical support:RBWL
Record No:苏ICP备2021015859号-1